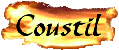
Blacksmithing
and Cutlery
by Gérard HEUTTE
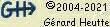

|
|
Hardening
|
Utility
Hardening is the most known heat treatment.
The fast cooling of steel makes possible to create a
very hard structure named Martensite.
The hardened steel is much harder than annealed steel, but also
more fragile.
The way for hardening (temperature, speed of cooling) depends on
the composition of steel and is very variable from one to another.
Hardening consists in heating delicately, the part above
the temperature of autenisation ("to dissolve" carbon and to form
austenite). This state is fixed by cooling steel
brutally. A large part of austenite is transformed then into
martensite. Not transformed austenite is called residual
austenite.
The range of ideal temperature is recommended by the
manufacturer of steel. "Hardenability" can be strongly modified
by the alloy elements. Hardening creates martensite, making
steel very hard. Attention, steel is then breakable and
requires tempering.
The quenching medium must be adapted to steel.
Thermal Cycle
Here is schematically the thermal cycle of hardening:

And various phases:
(1) Heating
The heating will be done at moderate speed.
The temperature of Hardening (TH on the graph) is specific for
each steel. It must be provided by the manufacturer.
(2) Stage
The temperature of hardening will be maintained
for a short moment, about one minute and a bit
more for the massive parts. The major criterion is to have a
homogeneous temperature. For hypereutectoid steels, the carbides will not be
completly dissolved, but that does not harm the quality of the
result. The not-dissolved carbides (placed in the grain
boundaries) could even avoid temporarily the enlargement of the grain
(information to be checked).
For the allied steels, it is advisable to refer to the
datasheet of the supplier to know the suitable temperatures.
(3) Cooling
Cooling should be fast and adapted to the
steel! If the cooling is a little too slow, Bainite will
be created. If cooling is too slow, steel will pass again in
Ferrite/Perlite/Cémentite form .
The speed of cooling is seldom provided, the manufacturers
rather specifies the medium of quenching advised (what is in general
enough).
Implementation
There still, a hardening oven can be very
useful (but not essential) for heating and the stage.
Heat steel at the temperature of hardening, then
maintained it the required time (approximately one or two
minutes). This operation could be done directly in the
forge. In a coal forge, move the
blade in the fire for a complete and homogeneous heating.
Use for that small gauge (maximum 10x20) charcoal
in order to have the most homogeneous possible heat.
Do not put directly the part in a violent fire.
It should, on the contrary, not be maltreated. Put
it on the side of the fire then let it warm gradually towards
600°C then a little more quickly at the good temperature.
Start with the edge on top and heat initially the
zone of the ricasso.
The loss of magnetism of the blade is in general a good
indicator for the temperature for hardening. In practice,
attach a magnet at the end of a string. If it does not
deviate any more with the approach of the blade, the temperature is
correct.
There are also pens with a special ink which liquify at a
precise temperature.
As soon as the blade is at the right temperature, remove it
from the forge with tongs for hardening. Proceed
quickly, but without precipitation. Plunge the blade edge
in first in the bath of hardening. Make longitudinal
movements until total cooling.
For air hardening, you can put the blade in the air flow
of a large fan.
See also the page about
quenching mediums
.
Opposite: Quenching in goop.
The tempering must be made as soon as possible.
Concept of hardenability
Druing hardening, cooling is done by the
outside of the part. According to the composition of steel,
this cooling will thus be propagated more or less easily and more or
less deeply! The hardenability of steel is its aptitude to
propagate the hardening from external surface towards the heart of the
part.
A steel with a low hardenability will take only superficially
hardening. A steel with a high hardenability could be hardened
in-depth.
The hardenability of steels is improved by the alloy elements,
mainly Chromium and Nickel.
Notes
> The main risks at the time of hardening are
the cracks and the deformations. A steel fissures if its form
presents weak points (sharp angles = rupture starts) or if the medium
of hardening is inadequate (too much hard). In this case, the
part is good for the dustbin. The deformations are generally
consecutive to an asymmetrical forging or an insufficient annealing.
Certain deformations are retrievable, but there is always a
risk of breaking!
> Always check hardening by a file stroke on the hardened
parts. The file must slip without hanging by producing a clear
sound.
> After hardening, the blade is very hard, but also
very fragile. A fall or a brutal handling can break the blade!
| | |