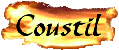
Blacksmithing
and Cutlery
by Gérard HEUTTE
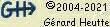

|
|
The forge fire
|
What could be more common than a fire in a forge?
But you have to understand its behavior and to
use it correctly... I will approach here only the traditional fire
of forge and with charcoal. Good reading and good
fire!
For recall, this site contains a page on
charcoal.
Principles
Here is what occurs during combustion.
(1) Under the action of heat, the carbon of the charcoal and
the oxygen in air combine to form CO (i.e. carbon monoxide):
C + O --> CO
(2) This carbon monoxide burns in releasing heat:
CO + O --> CO2
This reaction of creation of CO2 (i.e. carbon dioxide) is
accompanied by non luminous flames.
In fact this is the gas emitted by the burning charcoal that burns and thus creates heat.
Consequently, space is required between the
pieces of coal so that (1) the air (which brings
oxygen) circulates (2) the gases can be formed. From which the
importance of the granulometry of the charcoal.
In fire, you can distinguish several zones with different
effects:
Oxidizing zone:
close to the air flow, there is much (too much) of oxygen.
Combustion is in carbon deficit. This one will be taken
anywhere including in steel.
This zone extends on a few centimetres around the exit of
air. It is strongly disadvised working in this zone which
degrades steel. It is also the hottest zone of fire!
Neutral zone: A little
further from the air flow, combustion is relatively balanced.
The oxygen contribution corresponds about to the needs.
Reducing zone: Still a little
further from the air flow, combustion is in light oxygen deficit.
Steel can then collect the surplus of
carbon available.
Cold zone: Beyond about ten
centimetres, combustion is partial. The temperature is well too
low to effectively heat steel until the temperatures of work.
Heat steel
To heat steel under good conditions, some
guiding principles must be respected:
- Start gently.
Pose the rod or the part to be heated near the hearth
(e.g. nearby or on top of fire) while the preceding part is
finished. Then, place the part on
top of the hearth, with a soft ventilation for a calm fire. The
rise in temperature will be slow and soft. Leave some time for
the crystalline transformations to be done "softly".
It is necessary to avoid the "methods" like:
Fire from Hell and bar directly in the oxidizing zone!
- Work at the limit of the Reducing zone and neutral zone.
Avoid the oxidizing zone imperatively.
Fit up the hearth
To avoid working in the oxidizing zone, it is possible to encircle the hearth
with a heightening, which enable to place a steel bar directly in the good zone,
simply by posing it!
You can fix in front of and behind the hearth a
refractory brick.
In general, a distance from 5 to 7 centimetres is correct.
Technical data
A charcoal forge fire makes
possible to reach high temperatures
easily, including the "welding white". This
temperature requires a good air flow!
Interesting reference: The embers of a charcoal fire
are in the neighbourhoods of 800°C to 850°C
(with no air flow, and after a short waiting time).
Decarburization
Unless working exclusively in reducing zone wich you are never sure at
100%, you will be confronted to this phenomenon.
The carbon atoms are relatively mobile in steel. In a
natural way, they go from the places strongly carburized towards the
least carburized places. The migration of the carbon atoms
depends on many parameters. The temperature is most important
of them.
In oxidizing zone, the temperature is very high and there is in
the neighbourhoods of the part an important carbon deficit.
Carbon thus will leave steel to return in combustion!
In the other zones, this phenomenon exists more or less.
It is considered that a normally forged blade is decarbonized
on 2 or 3 tenth of millimetres.
Consequently, it will always be necessary to keep a little
"fat" on the edge.
The left figure shows what you should not do: To
remove (at the time of grinding/polishing) the decarbonized zone (in light),
it will be necessary to remove "a important" width of the blade, while going
down at least to the red arrow.
On the right figure, it will be enough to decrease
the width of the blade from 3 to 5 tenth of millimetres to the blue
arrow.
In general, always keep a thickness on the edge of
about 0.5 millimetre. On the large blades, you can keep a
bit more, but it is mainly to keep a rigidity with the blade at the
time of hardening.
| | |